Monroe Parallel Plate Modules Increase Oil and Solids Removal in Existing API Separator
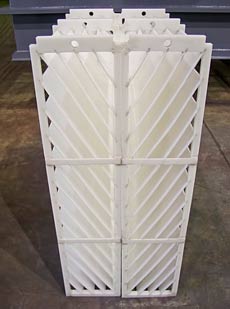
Challenge
A silicone manufacturing plant was increasing production capacity and needed to upgrade the treatment capability of the accompanying wastewater stream which contained tramp oils and solids. If possible, the plant wanted to increase the efficiency and capacity of two existing 140,000-gallon API Separators to handle the additional wastewater. The plant required that the water be clean enough to be recycled back to the manufacturing process.
Each API unit was 20 ft. wide and 100 ft. long. The flow rate needed to be increased from 950 GPM to 1,350 GPM.
Solution
Monroe engineers decided that a retrofit of the existing API Separators with modular laminar plates would successfully increase the throughput efficiency of the 140,000-gallon separators. The existing separators were modified to include the following:
- Diffusion wall with reaction jets
- UV-resistant polypropylene modular laminar plate cartridges
- Underflow outlet weir
- V-notch overflow weir
Solids would be collected in the conical inlet section and pumped out for proper disposal. Entrained oils would be collected by the modular laminar plates and would rise to the top of the separator. Separated oil would then be skimmed from the surface for disposal.
Result
The modifications allowed the plant to increase its flow rate as desired. Virtually all of the solids and oils were now being removed from the process, which allowed the process water to be recycled without attention. Since there were no moving parts, the system required minimum maintenance and could operate for extended periods of time when required.