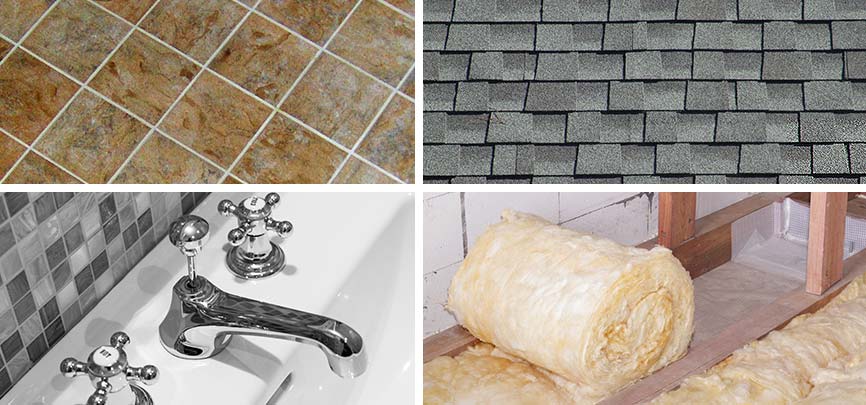
Environmental Solutions for the Building Materials Industry
Environmental Solutions for the Building Materials Industry
Water, wastewater, and air pollution control systems for manufacturers of building materials
Water, wastewater, and air pollution control systems for manufacturers of building materials
Application or technical questions?
Monroe Environmental has been supplying environmental control systems for manufacturers of industrial, commercial, and residential building products for over 50 years. We have installations controlling air emissions and treating wastewater streams at many of the largest production plants in operation. Monroe’s application specific approach can help solve the most challenging environmental problems for nearly every type of manufacturing process.
The National Emission Standards for Hazardous Air Pollutants (NESHAP) regulations apply to many sources of air pollution that are common to manufacturing of building materials including acid gasses, alcohols, metals, fine aerosols, particulate matter, and VOCs. Dryers, ovens, furnaces, boilers, and kilns used for production of bricks, tiles, and roofing products can emit many pollutants simultaneously, often requiring multi-stage emission control. Batch mixing, cutting, buffing, polishing, and finishing processes often produce particulate matter, aerosols, and fine dust requiring efficient capture and filtration to reduce and eliminate health risks to plant workers and the surrounding community.
Water treatment involves liquid streams from waste, rinse, and process waters often containing large quantities of oils, TSS, metals, and floating materials. Each of these constituents requires targeted treatment which can vary depending on production and application specific requirements. Water re-use and recycling is always a desired goal to minimize environmental impact and reduce operating costs. Proper separation, clarification, and filtration is required to make water re-use possible, and when not feasible, to ensure regulatory compliance for disposal or discharge.
Monroe Environmental has many successful installations for variety of manufacturing processes and applications, including:
- Glass production & cullet handling
- Fiberglass insulation
- Foam panels, boards, & cores
- Asphalt roofing products
- Kitchen & bath fixtures
- Lighting products (bulbs & fixtures)
- Brick & tile production
- Ceramic products
- Terra cotta, clay, & silica
- Textile production
- Wood products & laminates
- Flame lamination emissions
- Drywall & gypsum products
- Product safety testing oven emissions
- And many others
Monroe Can Help
Monroe Environmental has over 50 years of experience in designing and manufacturing a variety of Air Pollution Control and Water & Wastewater Treatment systems for the Building Materials industry.
Building Materials Manufacturing: Representative Projects and Systems for Pollution Control
800 GPM Thickener Clarifier to separate dense, sticky solids contained in the liquid stream at a gypsum manufacturing plant. Solids are now properly agitated and pumped out in a timely manner, preventing material setting that had previously damaged equipment and stopped production. Read More
High efficiency Cartridge Dust Collectors for brick and terra cotta manufacturing facility to exhaust mills and protect employees from exposure to crystalline silica dust. The plant had several material transfer and processing stations, each requiring a custom hood, ductwork, collector, and control system. Read More
40,000 ACFM Dual Throat Venturi Scrubber for collection of PM from insulation drying ovens. Unit was constructed of 304SS and included venturi scrubber with recirculation pump, integral liquid reservoir, chevron demister, drag conveyor for solids removal, fan, piping, valves, instruments, and controls.
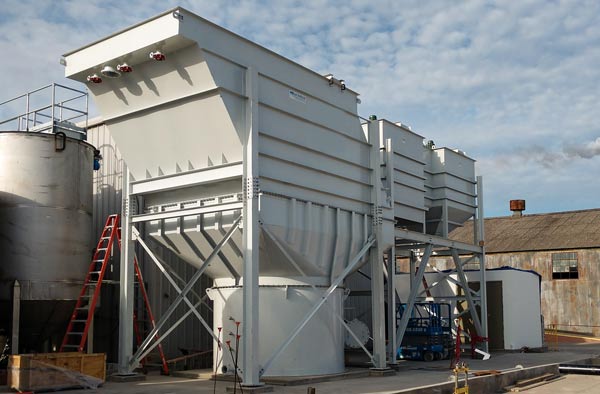
Vertical Plate Clarifier with three pretreatment mixing tanks to clarify process water at specialty insulation manufacturing plant. The system included an integral sludge thickener and was rated for 750 GPM.
2,500 ACFM Multi-Stage Scrubbing System for PM and acid fume (HCl/HF) capture from building material testing oven prior to RTO. The systems consists of a C-276 Quench Tower, FRP Dust Collector, Packed Tower Scrubber, pumps, instruments, and controls.
Multi-Stage Scrubbing System with Venturi Scrubber, Packed Tower Scrubber, and Water Clarifier for high efficiency scrubbing of the phenol, formaldehyde, and particulate from a batch reactor process at a fiberglass insulation manufacturing plant. Read More
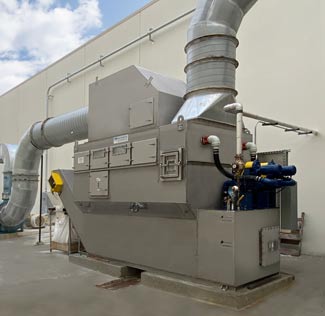
28,000 ACFM Venturi Scrubber, 304SS construction, for PM removal from FRP panel manufacturing process. The system included venturi throat, integral sump and separator, chevron mist eliminator, recirculation pumps, solids drag conveyor, and controls.
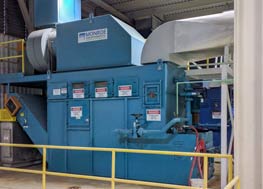
Dual Throat Venturi Scrubber to exhaust dryer for insulation and panel board manufacturing. The 18,000 ACFM unit with drag conveyor captures fumes and PM.
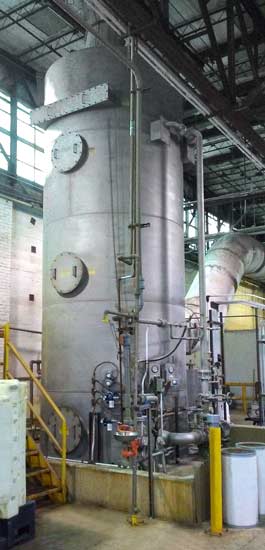
Wet Scrubber treats hot, nitric acid from the dryer at a ceramics plant. The 26,400 ACFM system can simultaneously cool the incoming gas temperature, control the acid fumes, and withstand the corrosive environment. Read More
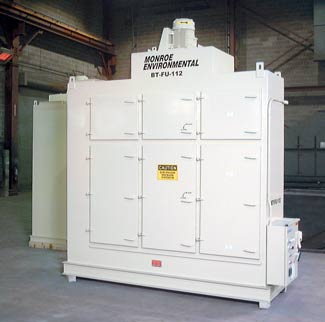
Multi-Stage Oil Mist Collector to remove heavy oil droplets, smoke, and sub-micron vapors for a synthetic fiber plant’s manufacturing operations. The four-stage system operates at >95% efficiency treating 0.3 micron sized particles. Read More
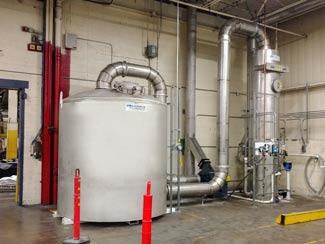
Multi-Stage Scrubbing System to remove H2S and VOCs from rubber vulcanizing process exhaust. System included Packed Tower Scrubber, Carbon Adsorber, ID fan, stack and ductwork, all 304SS construction and was rated for 3,000 ACFM. Read More
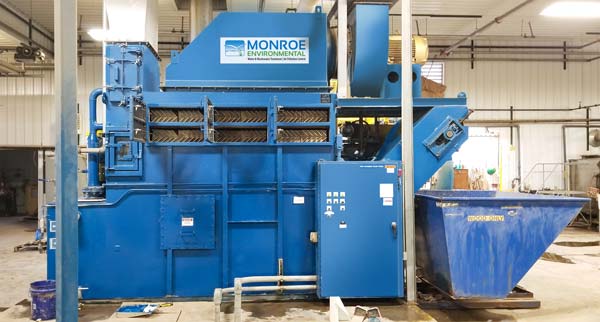
Dual Throat Venturi Scrubber rebuild for wood mill. After years of hard use, the scrubber needed some repairs. The venturi throat was replaced and upgraded, and all doors, gaskets, and required fasteners were replaced. New internal steel members were installed including chevron hold-downs, and repairs on the scrubber exterior were made before giving the entire unit a fresh coat of paint. The scrubber looks and operates like new after the rebuild.