Monroe Environmental Quench Towers and Condensers provide temperature reduction and control of hot process gasses through evaporative cooling, condensing, and a variety of heat transfer methods. A Quench Tower or Condenser is often the first step in conditioning a high temperature, polluted air stream so that particulate, acid gasses, metals, and other emissions can be adequately removed. Quench Towers and Condensers are often used following thermal treatment systems such as incinerators, reactors, kilns, boilers, furnaces, oxidizers, and other process systems that produce contaminated gas streams at elevated temperatures.
Monroe Quench Towers & Condensers
Monroe Environmental engineers have the experience to provide a customized Quench Tower design that will meet the needs of your application without the use of excessive water consumption. Using the air temperature and moisture content (lb. water per lb. of dry air), the temperature at full saturation can be predicted. Systems which require only partial saturation to meet specific temperature targets can also be designed by Monroe engineers.
Spray Quench Tower Design
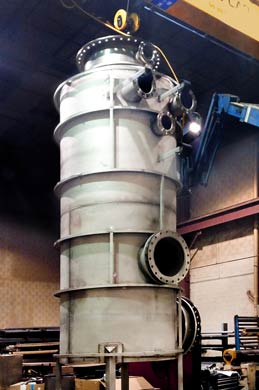
The proper design of a Quench Tower takes into account many factors, including:
- Inlet temperature
- Inlet moisture content
- Target temperature
- Target moisture content
- Effect of quenching on particulate formation and control
- Chemicals present is air/gas stream
- Velocity of the gas stream and gas retention time
- Nozzle design and spray patterns
- Materials of construction to withstand temperature and chemical attack
- And many others
Monroe Environmental can assess these and other application factors and custom design a quench tower that is suitable for your application.
Quench Materials of Construction
The materials of construction are especially important as they must be selected to both withstand attack from the various pollutants contained within the airstream and be resistant to high incoming temperatures. Common materials of construction include:
- Hastelloy
- AL6XN steel
- Duplex stainless steel
- 304 and 316 stainless steel
- Refractory and ceramic linings
- Other specialty alloys
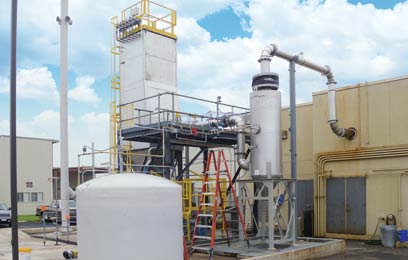
Quench Configurations
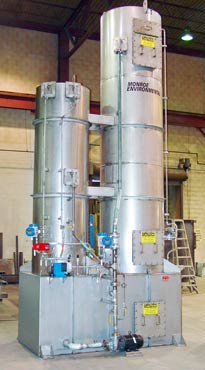
Vertical Quench Tower
A traditional vertical quench tower is the most common and widely accepted quench design. It is often similar in dimension and footprint to the downstream wet scrubber despite their operational differences. The incoming gas stream usually enters at the top of the tower and exits at the bottom or the side of the unit. Nozzles and spray patterns may operate in a co-current or counter-current mode depending on application specifics.
The vertical quench tower typically uses the recirculated scrubbing liquor and/or fresh water to evaporate moisture and cool the incoming gas. An emergency fresh water feed is usually recommended in the event of primary nozzle plugging or pump failure.
In this photo, the Quench Tower is on the left and the Packed Bed Scrubber is the tower on the right.
Inlet Duct Quench
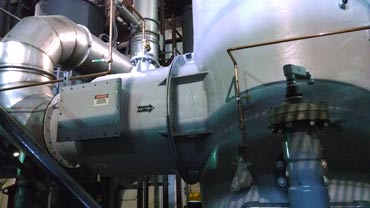
Inlet duct quenching can often be achieved when the inlet gas temperature is only moderately higher than the desired quench temperature and the gas is relatively dry.
A highly atomized spray at the inlet to a wet scrubber is often provided in this scenario.
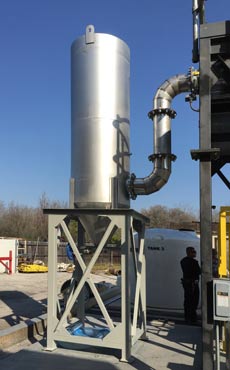
Dry Sump Quench
A dry sump quench uses a carefully controlled water feed to achieve partial quenching (not fully saturated) with no excess liquid in the quench sump, hence the name “dry sump quench”.
These units are needed when cooling is required but excess moisture will negatively affect downstream equipment.
Recent Projects
Quench Tower Applications
Pre-conditioning of gasses before scrubbers and other air pollution control technologies.
Treating off-gasses from:
Resources & Literature
Recent Case Studies
Air | Multi-Stage Scrubbing System for Incinerator Exhaust
Monroe Environmental provided a multi-stage wet air scrubbing system for HCl and particulate removal from incinerator exhaust at an industrial waste plant.