Cartridge Dust Collectors for Crystalline Silica Capture
Crystalline silica is a common product in a variety of industries, including ceramics, concrete, and others. During a manufacturing process, silica needs to be collected and removed from work stations and production processes in order to avoid build up and dispersal of high levels of particulate matter into the surroundings. If it is not collected properly, exposure to high levels of silica dust can be harmful to the health of people nearby.
On June 23rd, 2018 the Occupational Safety and Health Administration (OSHA) enacted laws to ensure that safe levels of silica are emitted into areas where people are present (Occupational Safety and Health Standards, Standard No. 1910.1053). OSHA required certain industries, including ceramics, to expose workers to no more than 50 micrograms of respirable crystalline silica per cubic meter of air as an 8-hour time-weighted average (TWA). By June 23rd, 2020 OSHA also requires that medical surveillance is available to people exposed to silica concentrations at or above 25 micrograms of silica per cubic meter of air as an 8-hour TWA.
Cartridge Dust Collectors Design Considerations
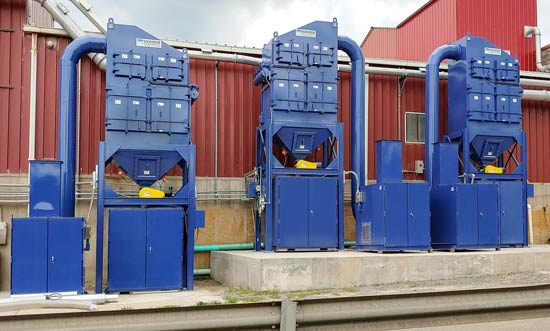
A cartridge dust collector is a common and efficient way to capture and remove silica from an operation that requires continuous collection. Application specific design criteria such as proper collector size, media selection, hood geometry, regular maintenance, heavy duty ductwork, and adequate airflow are critical to reaching the required dust capture.
Engineers must consider the abrasive nature of crystalline silica when designing and specifying a collection system’s components. Silica requires a high duct transfer velocity which increases wear from abrasion. Heavy gauge ductwork with long radius elbows and wear plates should be considered to maximize operable life. Additionally, dampers and other ductwork items should have appropriate linings, reinforcements, or wear protection to ensure long life under abrasive conditions. If budgets are restrictive of these types of enhancements, engineers should be aware that operating life may decrease and frequency of maintenance may increase.
Filter Media Selection
Filter media selection is also critical to proper design. Consultation with application engineers from media providers will inform the best selection – taking into account temperature, moisture content, silica load, filter cleaning design, etc. Slower velocities in the collector may help to reduce wear on the filters, however, this needs to be weighed in light of best practices for overall collector design (A/C ratio, inlet/outlet geometry, etc.)
With proper consideration given to the abrasive nature of the dust and its effect on control device design, Cartridge Dust Collectors can be successfully used for silica applications. Click the link below to see one such project.