Monroe Environmental provides custom engineered environmental solutions for a variety of steel industry and metal production processes. Our solutions are cost effective and of the highest quality for heavy-duty operations. Monroe has an impressive client list and a wealth of application experience within the industry, including pollution control systems for mills, mini-mills, smelters, casters, picklers, galvanizers, heat treaters, and many others.
We understand the unique challenges that steel producers and metal refiners face due to competitive forces, aging infrastructure, and strict environmental regulations. Our engineers assist with providing reliable environmental solutions by adapting trusted engineering principles to the specific treatment needs and process requirements of each plant and application.
Monroe Can Help
Monroe Environmental has successfully engineered, fabricated, and installed countless Air Pollution Control and Water & Wastewater Treatment systems for the steel industry.
Contact a Monroe Applications Engineer for assistance with your specific environmental challenge.
Steel Industry Experience: Representative Projects and Systems
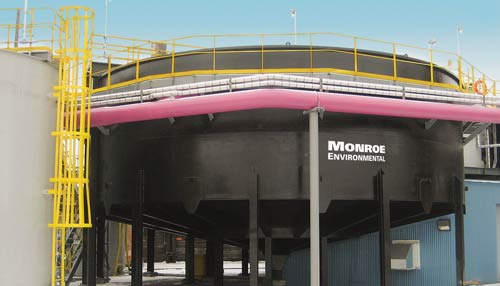
Circular Clarifier to remove TSS/fines from blast furnace scrubber wastewater. The 46 ft. diameter clarifier was elevated on legs for ease of access to sludge piping, and was designed to handle a 2,000 GPM max flow.
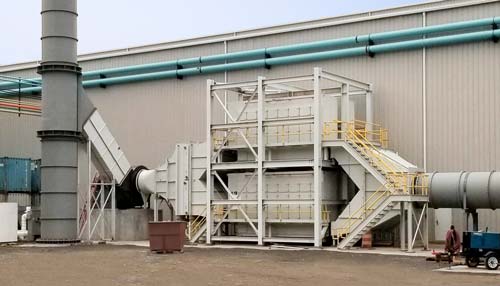
Multi-Stage Oil Mist Collectors capture oil mist, PM, and fumes from rolling mill exhaust. The systems was capable of removing filterable and condensable PM with high-efficiency filters and a cooling coil/heat exchanger with chiller. Read More
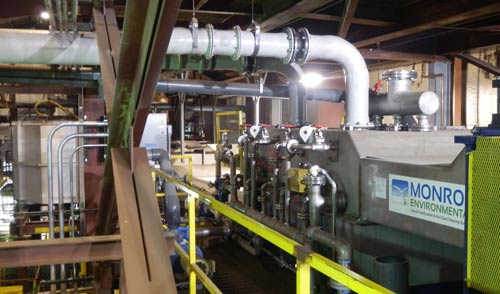
A steel coil galvanizing plant was in need of a new coil treatment line to meet higher material quality standards and maintain production. Monroe Environmental provided engineering, integration, and oversight services for the redesign, retrofit, and installation of the multi-million dollar steel coil cleaning line and wastewater treatment system. Read More
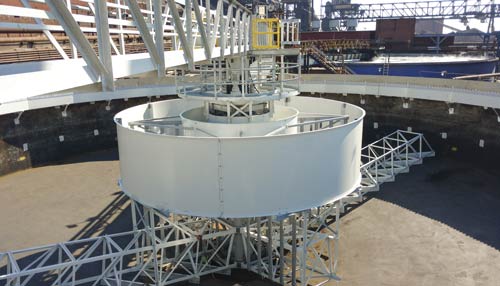
100 ft. diameter high-torque Thickener Clarifier treating blast furnace scrubber blowdown. The system included an inlet well flocculator, 500,000 ft·lbs drive torque rating, PLC controls, redundant sludge pumps, and a 15 mg/l effluent TSS and 5% solids underflow performance guarantee. Read More
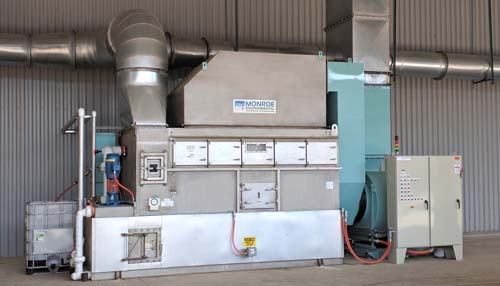
25,000 CFM Venturi Scrubber to capture and remove lubricant mist, particulate, and fumes from aluminum die casting operation. System included scrubber, fan, oil recovery unit, insulated liquid sump, and controls. Read More
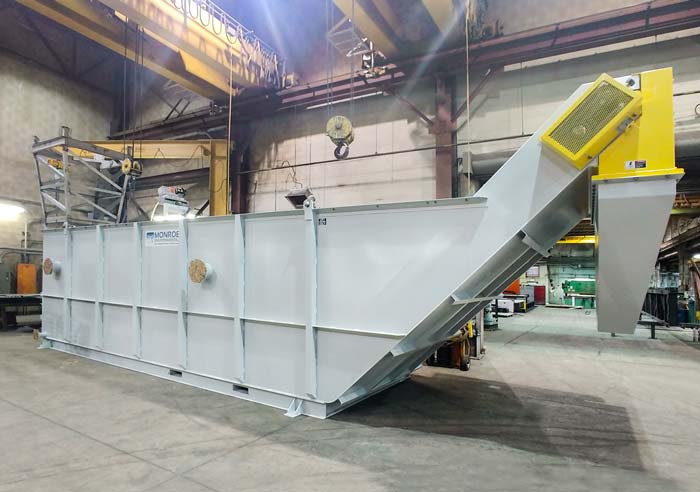
Drag tank for mill scale separation for steel tube mill. Chain and flight drag conveyor to capture and remove solids from mill water and a tube skimmer to remove floating oil. The system is rated for 660 GPM. Read More
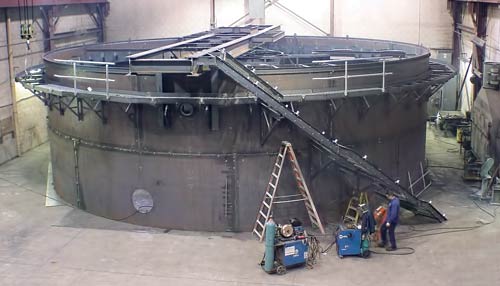
Circular Oil/Water Separator for primary treatment of waste oils and solids at a steel mill. The 50 ft. diameter clarifier was designed with low sidewater depth, inlet diffusion, and multiple skimming arms and collection troughs.
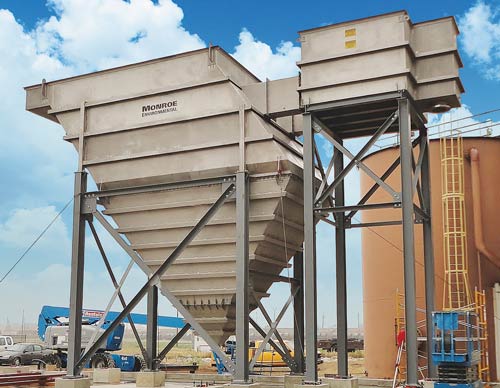
Lamella Plate Vertical Clarifier to remove iron and nickel hydroxides from metal finishing wastewater. The 1,533 GPM unit was constructed of 304SS, equipped with flash mixing and flocculation tanks, and provided over 3,900 ft2 of settling area.
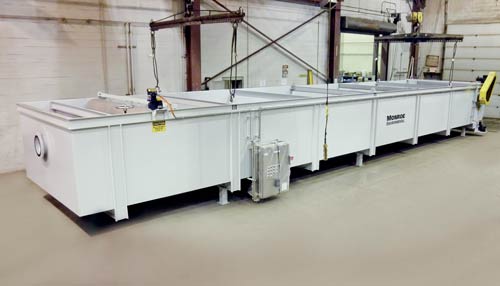
900 GPM API Separator for free oil separation prior to a DAF. The system featured inlet diffusion reaction jet baffles, chain and flight conveyor, and customized oil skimming system with collection beach and auger trough.
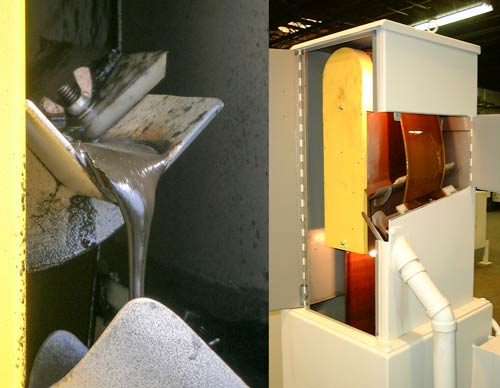
Monroe 8A Belt Skimmers for oil recovery from wastewater tanks at a steel mill. The custom thermoplastic belts are rated to withstand 180°F liquid temperatures.
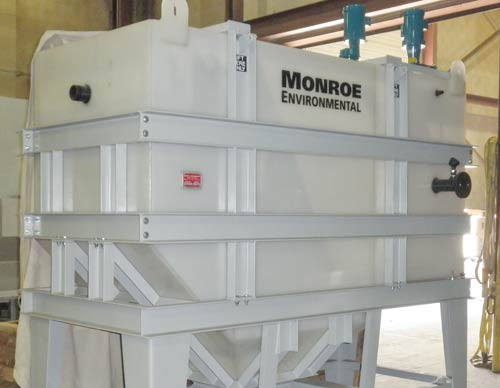
40 GPM Horizontal Plate Clarifier to remove TSS from pickling wastewater prior to membrane filtration. The polypropylene clarifier was equipped with chemical mixers, HDPE separation plates, and surface oil skimmer.
5,000 ACFM Packed Tower Scrubbing System to control HCl fumes from the pickling acid storage tank farm at a steel plant. Scrubber, fan, and discharge stack were constructed from FRP. Monroe also designed the tank farm ductwork and provided instrumentation and controls.